Asiabetking : The Ultimate Slot Game Platform and SBOBET Official Betting Partner in Indonesia
Asiabetking platform terbaik di Asia, khususnya di Indonesia untuk bermain game slot online. Daftar Asiabetking sekarang juga! Dapatkan bonus cashback member baru 100%, Garansi.
MENGAPA BERMAIN DI ASIABETKING?
- Akses ke Berbagai Permainan: Asiabetking merupakan pusat untuk berbagai permainan slot online. Gunakan 1ID untuk akses ke semua permainan.
- Potensi Kemenangan ("Gacor"): Istilah "gacor" sering dikaitkan dengan platform slot yang dianggap mudah memberikan kemenangan. Beberapa kali Asiabetking disebut sebagai platform dengan server "gacor" terpercaya.
- Kemudahan Akses Digital: Sebagai platform online, Asiabetking menawarkan kemudahan akses bermain kapan saja dan di mana saja.
- Promosi dan Bonus: Beberapa promosi dan bonus Asiabetking unik dan menarik. Ikuti perkembangan event di sini.
- Layanan Pelanggan: Layanan pelanggan super ramah melalui live chat 24 jam, yang penting untuk membantu pemain jika ada kendala.
10 Penyedia Game Slot Terkemuka Yang Ada di Situs Asiabetking
Ada banyak pengembang perangkat lunak yang menciptakan game slot online berkualitas tinggi. Beberapa penyedia yang paling terkenal sering dicari pemain Asiabetking:
- Pragmatic Play: Dikenal dengan grafis yang menarik, fitur inovatif, dan berbagai tema. Beberapa game populer mereka termasuk Gates of Olympus, Sweet Bonanza, dan Aztec Gems.
- PG Soft (Pocket Games Soft): Terkenal dengan desain visual yang memukau, cerita yang menarik, dan game slot yang dioptimalkan untuk perangkat seluler. Contoh game mereka adalah Mahjong Ways, Lucky Neko, dan Candy Bonanza.
- NetEnt (Net Entertainment): Pelopor dalam industri game online, dikenal dengan game slot yang inovatif dan grafis berkualitas tinggi. Starburst, Gonzo's Quest, dan Dead or Alive adalah beberapa judul populer mereka.
- Microgaming: Salah satu penyedia perangkat lunak kasino online tertua dan terbesar, dengan portofolio game slot yang sangat luas. Mereka juga terkenal dengan jaringan jackpot progresif mereka.
- Playtech: Penyedia besar lainnya dengan berbagai macam game slot, termasuk yang bertema film dan acara TV populer, platform live casino dan taruhan olahraga.
- Habanero: Dikenal dengan game slot yang responsif, grafis yang menarik, dan fitur bonus yang inovatif.
- Joker Gaming: Sangat populer di Asia Tenggara, menawarkan berbagai game slot dengan tema Asia dan fitur bonus yang menarik.
- Spadegaming: Penyedia lain yang populer di Asia, menawarkan game slot dengan tema budaya Asia dan gameplay yang menarik.
- Yggdrasil Gaming: Dikenal dengan desain visual yang unik, animasi yang halus, dan fitur bonus yang inovatif.
- Betsoft: Terkenal dengan game slot 3D sinematik mereka dengan cerita yang menarik.
OFFICIAL SBOBET BETTING PARTNER PIALA DUNIA 2026- ASIABETKING
SBOBET menunjuk situs Asiabetking menjadi official betting partner selama piala dunia berlangsung, dimulai dari klasifikasi hingga berlangsungnya bertandingan akbar tersebut. Sebagai platform taruhan daring yang memiliki reputasi global, Asiabetking dikenal memiliki riwayat kemitraan dengan berbagai organisasi olahraga dan klub sepak bola terkemuka.
SBOBET memiliki riwayat menjadi sponsor dan partner taruhan resmi bagi berbagai klub sepak bola, terutama di Liga Primer Inggris dan liga-liga lain di Eropa serta Asia, khususnya menjelang PIala Dunia 2026 ini.
Sebagai platform taruhan olahraga daring yang populer, menawarkan berbagai jenis pasaran bola (odds) untuk setiap pertandingan. Memahami pasaran ini penting bagi siapa saja yang ingin memasang taruhan. Berikut adalah beberapa pasaran bola SBOBET yang umum ditemui:
Jenis Pasaran Bola SBOBET yang Populer di Situs Asiabetking:
-
Handicap (HDP): Pasaran ini memberikan keuntungan atau kerugian gol virtual kepada salah satu tim sebelum pertandingan dimulai. Tujuannya adalah untuk menyeimbangkan peluang antara tim yang lebih kuat dan tim yang lebih lemah. Beberapa jenis handicap yang umum adalah:
- 0 (Bola Jalan/Draw No Bet): Jika pertandingan berakhir seri, taruhan dibatalkan.
- 0.25 (Voor ¼): Tim yang memberikan voor harus menang dengan selisih minimal 1 gol agar taruhan pada tim tersebut menang penuh. Jika seri, yang memasang pada tim yang memberi voor kalah setengah, dan yang memasang pada tim yang menerima voor menang setengah.
- 0.50 (Voor ½): Tim yang memberikan voor harus menang dengan selisih minimal 1 gol agar taruhan pada tim tersebut menang. Jika seri atau tim yang menerima voor menang, taruhan pada tim yang memberi voor kalah.
- 0.75 (Voor ¾): Tim yang memberikan voor harus menang dengan selisih minimal 2 gol agar taruhan pada tim tersebut menang penuh. Jika menang dengan selisih 1 gol, yang memasang pada tim yang memberi voor menang setengah, dan yang memasang pada tim yang menerima voor kalah setengah.
- 1 (Voor 1): Tim yang memberikan voor harus menang dengan selisih minimal 2 gol agar taruhan pada tim tersebut menang. Jika menang dengan selisih 1 gol, taruhan seri (dana kembali).
-
Over/Under (O/U): Pasaran ini memungkinkan Anda bertaruh pada total jumlah gol yang dicetak dalam suatu pertandingan, apakah akan lebih (Over) atau kurang (Under) dari angka yang ditentukan oleh SBOBET.
-
1X2: Pasaran paling sederhana, di mana Anda bertaruh pada hasil akhir pertandingan:
- 1: Tuan rumah menang.
- X: Seri.
- 2: Tim tamu menang.
-
Correct Score (CS): Anda bertaruh pada skor akhir yang tepat dari pertandingan. Pasaran ini memiliki odds yang lebih tinggi karena sulit diprediksi.
-
Half Time/Full Time (HT/FT): Anda bertaruh pada hasil babak pertama dan hasil akhir pertandingan secara bersamaan. Kombinasi yang mungkin adalah 1/1, 1/X, 1/2, X/1, X/X, X/2, 2/1, 2/X, 2/2.
-
Mix Parlay: Anda menggabungkan beberapa pilihan taruhan dari pertandingan yang berbeda ke dalam satu taruhan. Agar menang, semua pilihan dalam parlay harus benar. Keuntungannya adalah potensi kemenangan yang lebih besar karena odds dari setiap pilihan akan dikalikan.
-
Odd/Even (O/E): Anda bertaruh apakah total jumlah gol dalam pertandingan akan ganjil (Odd) atau genap (Even).
-
First Goal/Last Goal (FG/LG): Anda bertaruh tim mana yang akan mencetak gol pertama atau gol terakhir dalam pertandingan.
Cara Membaca Pasaran SBOBET:
- Tim yang Memberikan Voor: Biasanya ditulis dengan warna merah atau berada di bagian atas dalam daftar pasaran Handicap.
- Nilai Voor: Angka di samping nama tim menunjukkan besaran voor yang diberikan.
- Odds (Kei): Angka yang tertera di samping pilihan taruhan menunjukkan odds atau kei.
- Odds Hitam (Positif): Jika Anda menang, Anda akan dibayar sesuai dengan taruhan Anda dikalikan dengan odds. Contoh: Taruhan Rp 100.000 dengan odds 1.70, jika menang akan mendapatkan Rp 170.000 (termasuk modal).
- Odds Merah (Negatif): Jika Anda menang, Anda akan dibayar sesuai dengan taruhan Anda dibagi dengan nilai absolut odds. Jika kalah, Anda akan membayar sesuai dengan taruhan Anda dikalikan dengan nilai absolut odds dikurangi 1. Contoh: Taruhan Rp 100.000 dengan odds -1.10, jika menang akan mendapatkan Rp 100.000 / 1.10 = Rp 90.90 (belum termasuk modal). Jika kalah, Anda membayar Rp 100.000 * 1.10 = Rp 110.000.
FAQ ( Pertanyaan yang sering muncul) :
1. Asiabetking itu situs apa sih?
Asiabetking adalah sebuah situs platform daring yang menawarkan berbagai jenis permainan, terutama slot online. Situs untuk bermain game online gacor.
2. Apakah Asiabetking terpercaya buat main?
Bermain di situs Asiabetking, dijamin aman, kemenangan dibayar sepenuhnya. Data para pemain terenkripsi dengan metode canggih, anti bocor.
3. Game apa aja yang ada di Asiabetking?
Slot, Live Casino, Sportsbook, Togel, Arcade, Tembak Ikan, dan masih banyak lagi
4. Gimana cara daftar di Asiabetking?
Proses pendaftaran sangat mudah, klik "Daftar" atau "Registrasi" di halaman utama situs. Isi data diri seperti nama, alamat email, nomor telepon, dan pembuatan nama pengguna serta kata sandi.
5. Cara deposit sama withdraw di Asiabetking gimana?
Metode deposit instant tersedia melalui QRIS dan penarikan dana melalui transfer bank lokal, e-wallet. Informasi detail tercantum di halaman "Deposit" atau "Withdraw" situs resmi Asiabetking : https://ourbusinessnews.com/
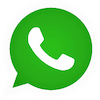
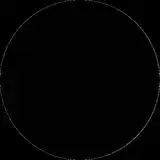
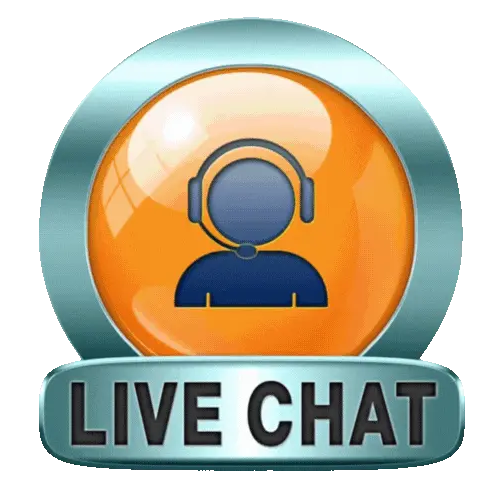